Date on Master's Thesis/Doctoral Dissertation
8-2015
Document Type
Doctoral Dissertation
Degree Name
Ph. D.
Department
Industrial Engineering
Degree Program
Industrial Engineering, PhD
Committee Chair
Stucker, Brent
Committee Member
Hardin, Tim
Committee Member
Murphy, Kevin
Committee Member
Pal, Deepankar
Committee Member
Yang, Li
Subject
Manufacturing processes; Three-dimensional printing
Abstract
Additive Manufacturing (AM) users rely on experiments and experience to predict the performance of AM processes. This trial and error approach for qualifying AM parts takes significant time and money. Simulation tools are an urgent need for today’s AM industry. One area of need is the automatic generation of optimized support structures based upon the scan patterns used to produce those structures. This research seeks to develop support structure generation tools based on real scan pattern and thermo-mechanical simulation tools for Selective Laser Melting (SLM) developed at the University of Louisville and being commercialized by 3DSIM, LLC. In order to benchmark the 3DSIM thermo-mechanical simulation tool, a thermal finite element model has been developed in ANSYS which uses the similar multi-scale meshing strategies as 3DSIM. The use of the sub-modeling approach for dynamic meshing was verified by comparing it against a uniform fine mesh model. The results of the two models match within an acceptable tolerance. Also, a mesh sensitivity analysis was carried out in order to show solution convergence as a function of increasing mesh density. The results of this analysis were also validated using experiments to show a match between experimental and simulated melt pools. Finally, the ANSYS solution was compared with 3DSIM results. The result of 3DSIM for a simple represented model is validated compared against the ANSYS model. What is more, it was significantly faster than their ANSYS counterparts for solving problems using a dynamic mesh. A scan pattern generation tool has been implemented to enable the input of real scan patterns as it is used in fabrication. The scan pattern is arbitrarily varied using user-defined parameters including hatching space, orientation angle, scanning start point, etc. Several types of scan patterns such as traditional S and chessboard are included in the tool. A simplified representation of the thermomechanical properties of support structures in order to accelerate the simulation of supports has been formulated. The effective thermal properties of support structures are represented using thermal homogenization. The effective thermal properties of the support structures have been found to be a function of their geometry, anisotropy and constituent independent thermal properties. The results from this study have been compared against standard models and a good match has been found. A novel framework for a support structure generation and optimization tool has been developed to overcome the difficulty of dealing with support structures in SLM. Supports are optimized and designed based on the thermal stress accumulated in parts as they are made as well as geometrical rules. The support structure is designed to be withstand the thermal stress at locations where it could cause damage to the part and support structure, while minimizing the overall need for support structure materials. The support structure is designed with non-uniform parameters so as to make it flexible to alter based upon thermal stress. Experiments were conducted to explore the threshold for block support structure parameters and results were applied to adjust and verify the tool.
Recommended Citation
Zeng, Kai, "Optimization of support structures for selective laser melting." (2015). Electronic Theses and Dissertations. Paper 2221.
https://doi.org/10.18297/etd/2221
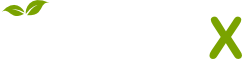
- Citations
- Citation Indexes: 1
- Patent Family Citations: 4
- Usage
- Downloads: 7296
- Abstract Views: 1300